
Dutch Bull is the owner of Solid Solutions. He is a 6-Sigma Blackbelt and foundry engineer with 37 years of foundry experience in iron foundries with 40 to 400 employees. He will work closely with your foundry engineer to collect the information needed to complete your project. Results will then be provided in a ready-to-use format, until optimal casting quality and cost are achieved.
The process involves running an initial simulation with Magmasoft software using information as provided by the foundry. The results will be analyzed to determine where porosity might exist in the casting, and if the proposed gating system can be improved in terms of soundness, yield or cleaning room costs. If changes are proposed, Magmasoft will again be used to verify the effectiveness of the revised gating system. The process will be repeated until all parties involved are satisfied the final design will offer the best chance for a casting of acceptable quality at the lowest possible production cost. At that point the final layout will be provided for the foundry to rig and sample the pattern.
The cost of this service can generally be recovered if just one re-gate and re-sample is eliminated from the new job startup process. When considering the savings in scrap, reduced startup time and reduced production cost, justifying this service is a no-brainer for efficient foundry management. Allow Solid Solutions to provide our consulting service just once, and you will always consider this evaluation to be an essential tool in your foundries toolbox.
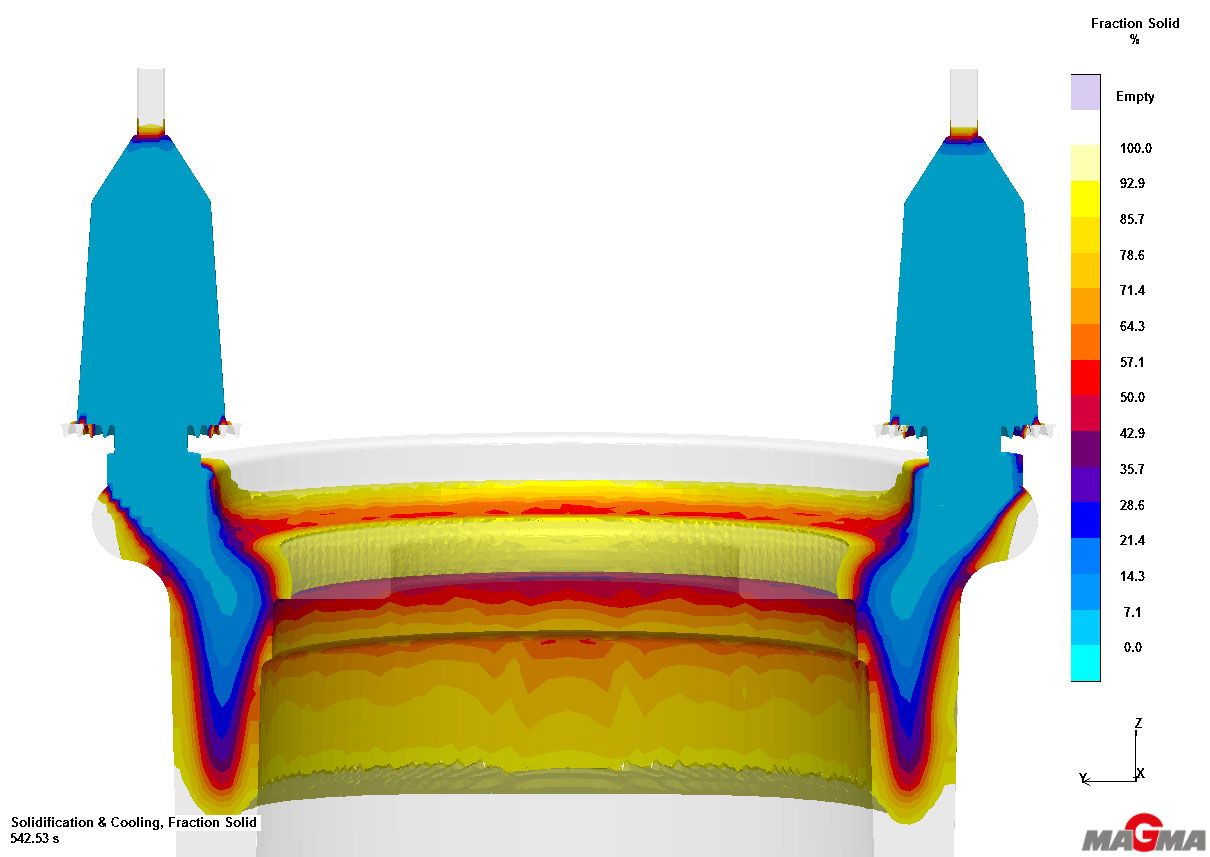
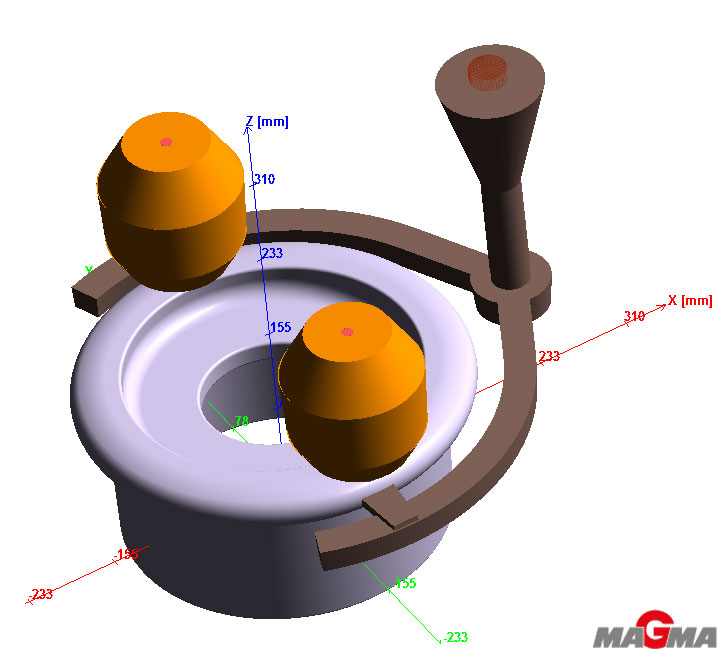
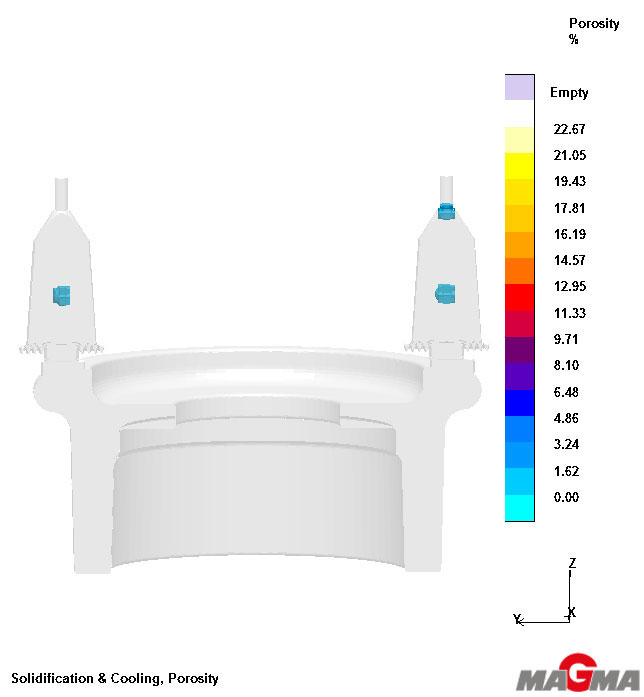